Skilled packaging machine repair service for business needs.
Why Timely Product Packaging Device Fixing Services Are Essential for Functional Performance
In the competitive landscape of production, the duty of timely product packaging maker repair service solutions can not be overstated. Such services are crucial not just for minimizing unexpected downtime yet additionally for promoting a smooth production atmosphere that meets customer demands. By addressing small breakdowns prior to they escalate, companies can considerably enhance functional efficiency and decrease long-term costs. However, the ramifications of neglecting these services prolong beyond immediate repair services, questioning regarding equipment integrity and general efficiency. What methods can firms apply to guarantee they stay positive in their upkeep method?
Impact of Downtime on Manufacturing
Downtime in manufacturing can be compared to a ship adrift at sea; without a trusted training course, manufacturing processes can quickly veer off track. The influence of downtime, particularly in packaging operations, can be both instant and significant. When machinery breakdowns, manufacturing halts, causing a backlog of orders that can strain consumer partnerships and credibility. Each minute shed translates into income loss, as business battle to fulfill market demand and satisfy commitments.
Moreover, unplanned downtime disrupts workflow, leading to ineffectiveness that reverberate throughout the supply chain. Staff members may be left still, resulting in lowered spirits and productivity. Additionally, the price of emergency situation repairs often exceeds that of arranged upkeep, further straining monetary resources.
In a competitive landscape, where time-to-market is vital, the ability to keep regular production degrees becomes extremely important. Downtime not only influences instant outcome however can likewise create a surge effect that affects stock levels, capital, and general operational effectiveness - packaging machine repair service. Hence, understanding and alleviating the impact of downtime is important for suppliers aiming to sustain their one-upmanship and ensure long-term development
Advantages of Routine Upkeep
Routine maintenance of product packaging equipments acts as a critical column in making certain undisturbed manufacturing and operational performance. By carrying out a constant upkeep timetable, organizations can considerably enhance the dependability and durability of their devices. Regular inspections enable the timely identification of damage, protecting against small problems from escalating into major malfunctions.
Additionally, regular upkeep maximizes machine efficiency, making sure that product packaging procedures operate at peak effectiveness. This optimization not only increases throughput however additionally decreases the likelihood of product issues, therefore preserving high-grade criteria. Properly maintained equipments contribute to energy performance, lowering operational expenses connected with too much power intake.
Along with efficiency benefits, regular maintenance promotes a much safer working atmosphere. By making certain that devices run correctly, the danger of accidents and injuries triggered by equipment failure is notably reduced. This commitment to safety and security not just shields workers however also aligns with regulative compliance, mitigating potential legal liabilities.
Inevitably, purchasing regular maintenance improves overall productivity, lowers unanticipated downtime, and advertises a society of proactive asset monitoring. This critical method guarantees that packaging operations remain competitive in a hectic market, which is necessary for sustained success.
Expense Ramifications of Postponed Repair Work
Disregarding prompt repair visit site services on product packaging equipments can cause substantial financial repercussions for businesses. When machinery breakdowns, assembly line can stop, causing lost output and postponed delivery schedules. packaging machine repair service. Each hour of downtime converts into not only lost sales but likewise potential charges from customers as a result of unmet target dates
Furthermore, postponed repair work can exacerbate existing problems, bring about a lot more severe damages and raised fixing expenses in time. A small malfunction might escalate right into a significant failure, necessitating expensive components substitute or a total overhaul of the device. This can strain budget plans and divert funds from various other crucial areas, preventing overall operational growth.
Furthermore, businesses may face raised labor expenses as workers stay still or are reassigned during expanded repair work periods. The longer machinery is out of service, the a lot more significant the impact on workforce efficiency.
Enhancing Equipment Long Life

Carrying out a regular upkeep timetable can recognize deterioration early, preventing little problems from intensifying into costly malfunctions. This aggressive approach not only enhances the device's operational integrity however additionally maximizes the total manufacturing their explanation process. Operators must likewise ensure that devices are made use of according to maker specs to prevent unnecessary stress and anxiety on important components.
Additionally, purchasing top quality substitute parts throughout repair work adds to tools longevity (packaging machine repair service). Using second-rate elements may cause constant breakdowns, negating any kind of expense financial savings understood from less costly repairs. Appropriate training for operators on ideal methods for maker handling and procedure can also considerably influence the tools's life-span
Selecting the Right Repair Service Service
Picking the suitable repair work solution for packaging machines is vital for making certain minimal downtime and optimal performance. When evaluating possible service suppliers, consider their industry experience and expertise in product packaging equipment. A company with a tried and tested performance history in dealing with similar websites tools will likely have the necessary competence to detect and deal with concerns efficiently.
In addition, examine the availability of service technicians and their response time to solution phone calls. A repair work service that offers 24/7 support can dramatically decrease the effect of unanticipated maker failings. Make inquiries regarding their upkeep programs, as positive service can protect against pricey failures and expand the life expectancy of your equipment.
Evaluate consumer evaluations and testimonials to assess the reliability and top quality of the service. A trustworthy repair work service ought to have a history of completely satisfied clients who can attest to their expertise and efficiency. Consider the prices included, consisting of parts and labor. While affordability is important, prioritize value-- making certain that the solution meets your functional demands without compromising top quality. By diligently selecting the right repair work solution, services can improve their operational performance and minimize disturbances in production.
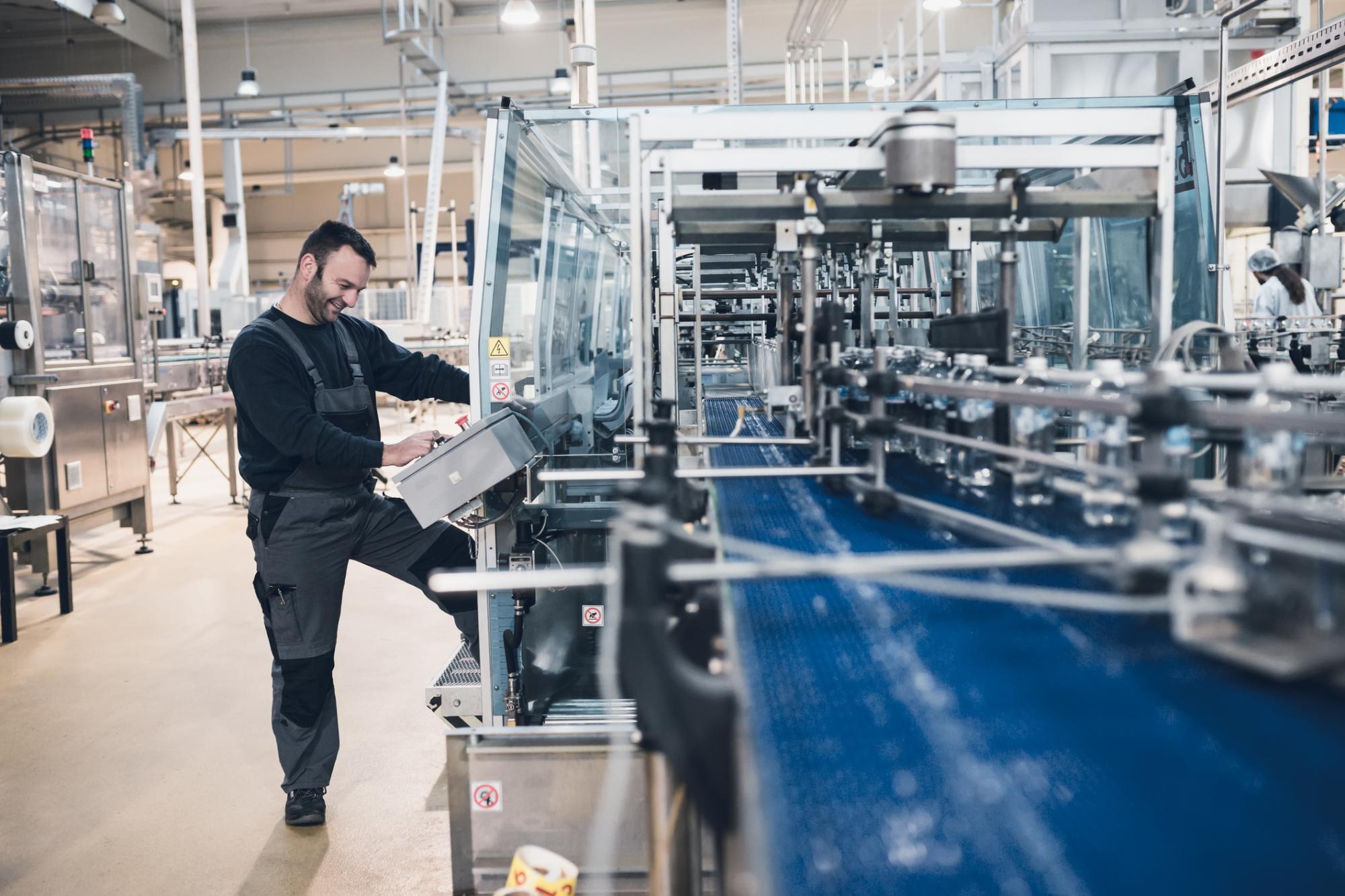
Verdict
Finally, timely packaging equipment repair solutions play a vital duty in maintaining functional efficiency. By decreasing unintended downtime, these solutions not only boost manufacturing circulation yet also add to set you back financial savings and improved tools durability. Normal maintenance and punctual repair work offer to minimize small concerns before they escalate, consequently making certain optimum equipment performance. Inevitably, prioritizing prompt repair work promotes a dependable supply chain, bolsters worker spirits, and raises customer contentment through consistent product distribution.